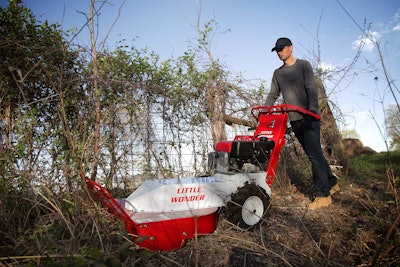
By Steve LePera
When you’re looking for new equipment, you want ROI and you want it fast. It often feels like the fastest way to get ROI is to buy the product with the cheapest price tag. It’s difficult to see past the sticker and think about the long-term operation and maintenance costs as well as opportunity costs and how a different investment might pay off in the end.
While parting with cash isn’t easy, investing in quality equipment pays dividends in reduced expenses later. This is especially true for equipment in the demanding debris management segment. Debris management equipment, such as a brush cutter, requires heavy-duty components and productivity enhancing features to tackle challenges like thick brush and tree saplings.
While cost is always a consideration, cutting corners on value-added features is seldom worth the savings, and it’s better to look at a lifetime cost verses a short-term purchase price. If investing a little more means extending the life of your equipment by a year or two, or being able to tackle a wider range of jobs, it’s well worth the added initial cost.
Plus, when it comes to increasing productivity, features that make maintenance easy keep machines on the jobsite, not in the repair shop. That’s why it’s important to do the research and select a brush cutter built to achieve long-term profits and exceptional productivity.
Making the cut
Start the selection process by determining what type of debris the machine will face. Brush cutters are designed to take on certain heights and thicknesses of brush, and if that is exceeded, it can cause damage to the machine. It’s far better to err on the side of caution by selecting a brush cutter capable of taking on multiple jobs and thicker brush than purchasing a smaller unit that might save you money, but will also limit versatility and opportunity.
Tough jobs, such as clearing vacant lots and establishing trails or paths, require a brush cutter that tackles weeds, heavy brush and overgrown vegetation. Look for a model capable of taking out saplings up to a couple of inches thick and won’t shy away from chest-high weeds. After all, if the brush cutter can’t handle that, it’ll be back to the branch clippers to finish the job.
An efficient machine is capable of clearing an acre of brush or more per hour, which enables contractors to quickly complete the project and move on to the next. To help achieve maximum productivity, consider brush cutters that feature a hydrostatic drive with clutchless variable operating speeds as opposed to a unit with gear selection.
Hydrostatic drive allows the operator to simply squeeze the handle to control both speed and direction for easy and intuitive operation in varying worksite conditions, such as when moving from open green spaces to thick overgrowth.
Also, consider if the brush cutter uses cables or solid rods to connect the transmission, parking brake and blade clutch. Models with cables add the risk of branches getting tangled in and breaking the cables, stopping the job. Solid rods are much more durable to withstand the demands of thick underbrush and keep contractors productive.
Never skimp on key features
Be sure to cover the basics first. For instance, look for a unit with a wraparound hand guard that runs along the handlebars and front of the machine. This shields the operator during operation. Some units only have a small hand guard covering the handle grips, but this fails to protect from brush that reaches the operator from the front of the machine.
Next, focus on the deck of the brush cutter, which is the most important feature. Look for a brush cutter with a heavy duty steel cutting deck and steel front deck plates. These are individually mounted hinged plates that hang down from the front of the cutting deck.
They allow the brush cutter to easily move over brush and keep the brush in the cutting zone. Be sure to consider the construction of the protective front deck plates at the time of purchase. If this were a grass mower, a rubber flap would be fine. However, brush cutters tackle thick, heavy brush often in overgrown areas with little or no visibility of what lies beneath. It’s best to trust the durability of steel plates over rubber flaps or hanging chains.
Today’s brush cutters can operate at a pretty fast pace. Sometimes it’s best to slow down. This is especially true when working on unfamiliar or obstructed terrains where operators cannot easily track the contours of slopes and hills.
While a hydrostatic drive is quick to react and smooths speed adjustment for the operator, a speed limiting setting on the machine can help avoid overdrive situations altogether. Brush cutters with a speed limiter can set a maximum running speed for optimal control. Look for a unit with a dial configuration, as this will give the greatest level of speed control flexibility for on-the-fly adjustment as conditions warrant.
Lastly, check if the brush cutter features a parking brake. It’s a simple but important feature that minimizes the risk of the machine not staying in place when work is halted on a hill or sloped area.
Built to last
Brush cutting is tough work. That’s why it’s important to invest in a machine that’s built to last. Look for a unit constructed of heavy-gauge steel at least where it matters; the deck, skid shoes, push or knock down bar and handle area.
When clearing brush, the unit selected is only as good as the knock down bars that feed the blade. Though they might look alike, they are not created alike. Be sure to choose a machine that features heavy-gauge solid steel push bars rather than those made of thin-gauge steel tubing. The hollow tubes easily dent and bend, reducing its effectiveness and increasing the need for replacement.
In addition, inspect the quality of the unit’s skid shoes. These are steel bars or rods connected to the left and right front deck feet. Similar to push bars, skid shoes made of hollow tubing dent easily and require frequent replacement. Instead, solid steel skid shoes will hold up much longer and provide excellent flotation over rough terrain because the steel withstands damage from brush, rocks and low lying stumps.
Also, select a brush cutter with durable tires. Pneumatic tires are common, but they are susceptible to puncturing. Since they cost roughly $90 to $140 to replace, costs can quickly add up. Alternatively, puncture-proof foam-filled tires are designed to endure the most challenging work conditions with the ability to withstand punctures from brush, nails, glass or other sharp items so the tires rarely need replacing.
In addition, look for deep tread or bar tread tires for added traction when moving across overgrown grasses and weeds and tackling undulating terrain. Some manufacturers offer foam-filled tires standard at no additional cost, while others charge a hefty premium for this tire option.
Easy or excessive
Never overlook maintenance requirements when selecting a brush cutter — an easy thing to do when blinded by a cheap price tag. The cost of replacement parts and the labor time to fix a brush cutter quickly add up, making the unit’s initial price deceiving. Plus, there’s bound to be lost profits when contractors turn down jobs while their brush cutter is in the shop.
Look for machines designed to simplify maintenance. For example, some manufacturers design the equipment to call attention to greasing points for maintenance technicians. This ensures that technicians can easily locate the grease points and don’t forget to maintain these areas. It may seem small, but this feature helps to achieve the brush cutter’s full service life.
Welded or bolted components also impact maintenance time. For example, wearing components that are bolted, instead of welded, to the brush cutter make it easy for technicians to gain access and replace individual parts. Alternatively, welding requires replacing even more parts, such as the entire cutting deck to make a spindle replacement.
This quickly gets expensive since a cutting deck costs around $200 to replace. When looking to stretch investments a little further, select a unit that uses reversible blades to double the blade life. This simple feature saves $25 per blade replacement, which quickly adds up over the life of the unit.
After sales support
After looking over the brush cutter, there’s one more important aspect to consider: the manufacturer. Is it reliable?
A good indicator is a proven history of developing quality products. Read online blogs and reviews to see what customers say. It’s also important that the machine includes a warranty and a broad servicing dealer network to ensure you can get ready service of the brush cutter if needed.
For additional resources, check the manufacturer’s website for online videos and information on the brush cutter as well as easily accessible support for troubleshooting or ordering spare parts. That combination ensures contractors know not only how to effectively use and maintain the equipment but also that they will get help quickly when it’s needed.
Choosing a quality brush cutter from a reliable manufacturer yields long-term rewards. Although contractors originally front a few extra bucks for value-added features, it pays off. Between time saved on maintenance and repairs, operators soon make up for the initial cost. Remember, the right manufacturer and machine make the cut for long-term results.
EDITOR’S NOTE: Steve LePera is the director of marketing for Little Wonder, Mantis and Classen — three brands of Schiller Grounds Care, Inc., a Pennsylvania based manufacturer of outdoor power equipment.