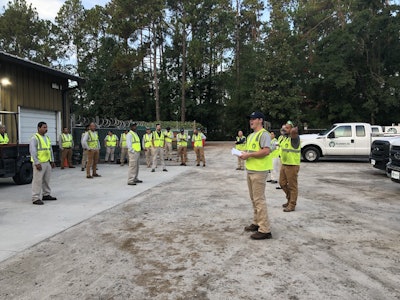
Photo: Jill Odom/Total Landscape Care
The landscaping field harbors a number of work hazards, and simply saying you’re committed to safety isn’t enough to keep your crews safe day in and day out. You have to walk the walk and have a true safety culture to protect your employees.
“A safety culture is extremely important because our primary responsibility is for every employee to arrive home safely every day,” says Fred Peratt, owner of Environmental Enhancements, based in Sterling, Virginia. “Safety promotes professionalism to our clients, suppliers, subcontractors and employees, which shows we care as an organization.”
Creating a strong safety culture allows you to take the practices covered in your safety program and turn them into a way of life for your employees.
Some of the benefits of having a safety culture include lower insurance premiums, less downtime thanks to fewer injuries, reduced equipment damage, minimized vehicle accidents and pride of ownership with all employees.
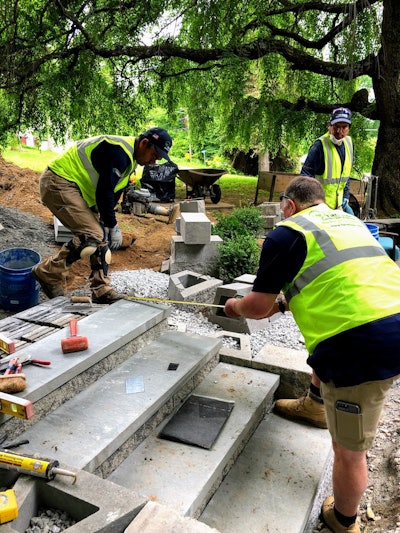
Photo: Farmside Landscape & Design
“Guys will pause and understand what they’re getting themselves into before a bad situation gets worse,” says Miles Kuperus Jr., CEO of Farmside Landscape & Design, based in Wantage, New Jersey. “The older fellows who have been with us a number of years have very good safe practices and they’re constantly nurturing the younger hires that we bring on.”
What’s important to understand about safety culture is it is never something you can check off your list.
“It’s a culture; it’s something you never arrive at being a perfectly safe company,” Kuperus says. “It’s a journey and about constant improvement.”
Kyle Snow, a manager with Snow & Sons Tree and Landscaping, based in Greenfield, Massachusetts, adds that some may think it’s too expensive to devote the time needed to create a safety culture.
“Truthfully, the return far outweighs the costs from lower insurance, improved quality and improved efficiency,” Snow says.
If your landscaping company truly wants to cultivate a strong culture, where you should start developing your program depends on your company, the current culture and the people involved. However, no matter what phase you’re in, the dedication to safety has to start from the top.
“You can’t just say you have a safe culture without really implementing it throughout your organization,” Kuperus says. “It’s got to be from the top down. The misconception would be you say, ‘I want to have a safe culture,’ but the boss doesn’t implement it. The person that owns the company really has to believe in it and move it down. It can’t be from the bottom up.”
While the leader has to get the ball rolling, forging an effective safety culture requires commitment from everyone in the organization.
“Expectations need to be set from the beginning and then consistently followed,” Peratt says. “Every employee has to be held accountable for the implementation of safety, which creates the culture. No surprises and no excuses.”
Snow says more communication and constantly demonstrating the importance of safety would be a good place to start if it’s not already being done, as well as having more focus on training and development. He says his company is constantly working to improve its overall safety and training.
“Through initial training and ongoing in the field training. we are able to provide a good foundation,” Snow says. “Crew foremen are also excellent at assuring team members (especially new ones) are following the proper methods and procedures, which helps prevent overall accidents. Our goal is to train new team members at their pace so that we don’t put them into a situation that they are not prepared and ready for.”
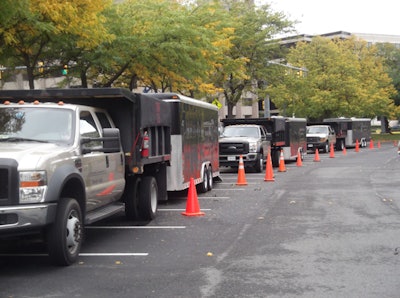
Peratt advises starting with your insurance company and having them do a thorough safety audit to identify areas where you are doing well and where you need to improve.
Landscapers can also take advantage of the numerous resources available to them, such as the ones provided by the National Association of Landscape Professionals (NALP) that you can view here. NALP also offers a Safe Company Program that provides a manual on creating a safety culture and shows your commitment to safety.
Having regular safety meetings can also keep proper practices top of mind, but the frequency to hold them depends on what works best in your specific company.
For Snow & Sons, they have safety meetings bi-weekly and discuss it regularly in common areas, while at Farmside Landscape & Design, they find weekly meetings work best for them. Kuperus says these 15- to 20-minute meetings every Tuesday are a good time to discuss their near misses and direct hits.
“We talk about safety in our daily huddles and have monthly safety meetings with the entire company,” Peratt says. “Safety needs to be practiced daily and it does not have to be a meeting, just a gentle reminder. We always say that ‘What you inspect is what you expect.’”
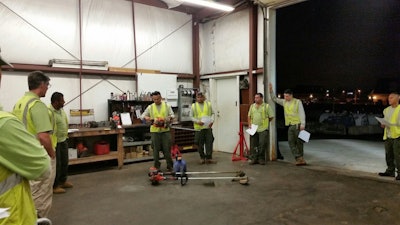
Photo: Environmental Enhancement
As for who should lead these meetings, what works best, again, varies company to company. Peratt says it is the owner, account managers and project managers who focus on training during the morning huddles, while it the responsibility of the crew managers to train their teams on proper safety practices every day.
“In our case, most of the time it’s the managers of the divisions,” Snow says. “We do encourage feedback and are always willing and happy if someone (any team members) wants to conduct a safety meeting or even discuss a certain topic at one. Since we don’t require this, it doesn’t happen too often. I think the more people you can get involved the better.”
At Farmside Landscape & Design, Kuperus says that one person will be responsible for creating the safety curriculum that year and someone new will take on that role the next year. During the weekly tailgate talks, various employees are nominated to lead them.
When it comes to accountability, positive reinforcement is always preferred. Kuperus says it is best to coach when accidents occur and figure out what went wrong, rather than come at it from a disciplinary standpoint, as employees are less likely to be open and transparent about near misses in the future.
“You got to be careful that you don’t go from a discipline side,” Kuperus says. “That was never our intent. Our intent was to create a positive culture and what I always tell the guys is the last thing I want to do is go to your doorstep and tell your wife that we had a non-safe practice in our company that killed your husband or something like that. That makes me lose sleep at night, but if I know our guys are doing the best we can, if something happens, we know that we’ve done our best to train our guys in safe practices.”
Snow adds that if positive reinforcement doesn’t work, it may require a different conversation.
“Even in this case, I wouldn’t call it negative or punishing reinforcement,” Snow says. “More trying to figure out what the problem is and why it keeps happening and isn’t getting corrected. Then, come up with a plan together to correct it.”
If there are employees who don’t buy into the culture of safety, Kuperus says they don’t stay with the company. Snow says they strive to train and work with them, but if it’s clear nothing is going to change, the employee almost always leaves on their own.
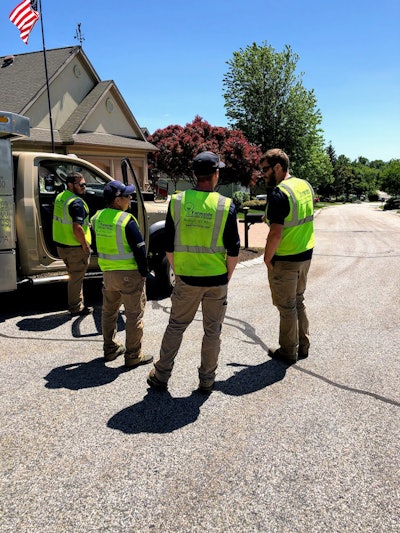
“We have learned that when mistakes occur, or someone is not buying into the culture that it is a great learning opportunity for the employee and the company,” Peratt says. “We will go down a list of questions to help solve the issue. Are we not clear on our expectations? Was this missed in our onboarding process? Do we need to slow down and take a different training approach? We find that open communication and transparency are difficult and always needs to be monitored for improvement.”
One of the ways to measure how successful your company has been with its safety culture over the year is to participate in safety recognition awards like those held by NALP.
Snow & Sons received the “Best of the Best” award from NALP last year, which is awarded to landscaping companies who have maintained the Overall Safety Achievement award – gold level status for three consecutive years.
Environmental Enhancements earned the Overall Safety Achievement award – gold level and had no vehicle accidents and no days away from work as well in 2019. Meanwhile, Farmside Landscape & Design also had no days away from work, no injuries or illnesses, a silver level Overall Safety Achievement award and had the most improved employee safety.
Amy Easterday, manager of programs and events for NALP, says the most improved employee safety award is given to the company that has the highest percentage increase over the previous year’s contestants.
The data used to calculate the company’s employee incident rate is based on the total number of: employees, hours worked, injuries and illnesses, days of job transfers/restrictions and days away from work.
None of these companies use the safety awards as a form of motivation for their employees, but rather as a way to recognize their staff for a job well done.
“I think we’re motivated as a company, as owners, to achieve that and then we bring it back for our staff and show them the national recognition,” Kuperus says.
For those interested in entering, the NALP Safety Recognition Awards are open through May 30, 2020.