Phoenix landscaping company conducts plant density study to optimize water consumption, tries mobile mapping to collect ‘Big Data’ quickly
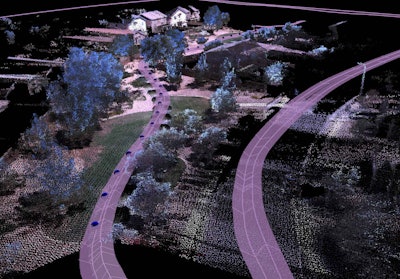
When the public thinks about landscaping, high tech doesn’t immediately come to mind. After all, this is work involving dirt, manual labor and plants. Mechanical engineering is represented in the form of a backhoe loader, for example, but that’s about as “technological” as the industry gets. Right?
Actually, anyone inside the industry would tell a different story. This is a field characterized by large inventories and a wide range of variables affecting product and service quality, starting with weather and soil. The convergence of these variables creates the need for a great deal of monitoring of growth. As a result, any landscaping company that seeks to be profitable over the long haul without relying on data for botanic maintenance decision-making probably should.
For a landscaping company that does business in the Desert Southwest such as DLC Resources in Phoenix, the need for monitoring is even greater due to the harsh environment.
The area receives only about 8 inches of annual precipitation on average, so optimizing the volume of water used for irrigation, for example, is a high priority for landscapers.
For years, DLC Resources has embraced technology by employing geographic information system (GIS) databases for purposes of inventorying and monitoring thousands of plantings at numerous properties that it manages in the area. Its certified arborists have relied on these data to schedule optimal tree maintenance.
But DLC Resources has sensed an opportunity to improve its processes. In this case, an arborist occasionally visiting a site to sample tree condition is one thing—going from site to site and inputting data for every single growing thing into a handheld data collector is another.
Recently, DLC Resources conducted a pilot study of plant densities at one of its properties to evaluate the water demand of several plant species in the dry climate. At the same time, it was a technology pilot project: the company has taken technology adoption to another level in an attempt to improve data collection efficiency and increase the robustness of its GIS data.
Mobile mapping
In spring 2012, two professionals at RDO Integrated Controls (RDOIC), a dealer of Topcon Positioning Systems equipment and a division of RDO Equipment, approached DLC Resources with a potential solution for improving the efficiency of gathering data from its considerable inventory.
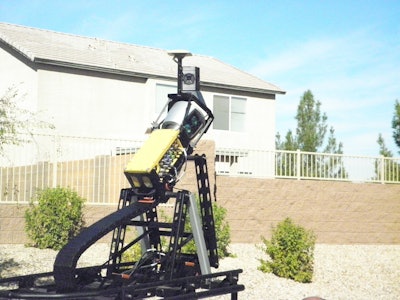
Product Specialist Nik Smilovsky, MS, GISP and Survey Account Manager Yon Egusquiza, introduced DLC Resources to the idea of using mobile mapping technology to collect “Big Data” and build an even more robust GIS database of the landscaper’s properties and plantings.
For that purpose, RDOIC uses Topcon Positioning Systems’ IP-S2 HD system. The system, which RDOIC mounts on the back of a pickup truck, consists of a dual-frequency, dual-constellation Global Navigation Satellite System (GNSS) receiver that establishes the geospatial position of the vehicle; an inertial measurement unit (IMU) that tracks vehicle attitude (pose); a long-range Light Detection and Ranging (LiDAR) sensor head equipped with 64 lasers that captures high-resolution, high-density point clouds at up to 100 meters away that are time-stamped using special software; and external wheel encoders that capture odometry data from the vehicle. In addition, a high-resolution digital camera captures 360-degree images.
Every second, the scanners collect 1.3 million x, y and z points that are used to obtain accurate geospatial positions for assets. Integration of these technologies creates a three-dimensional position for the vehicle and provides accurate tracking in challenging or denied GNSS environments. A laptop computer inside the truck uses a web browser to communicate with the bed-mounted equipment via an ethernet cable; data collection does not require an Internet connection.
While en route to a property in the southwest valley of Phoenix that DLC Resources manages, Smilovsky pointed out that the company’s mobile mapping pilot project strongly indicates that it is an early adopter of the latest GIS technology. A plant density study that used mobile mapping follows the spirit of DLC Resources’ WaterRight Program, designed to make better water management and budgeting projections.
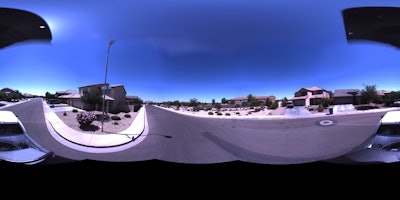
At the property, Danielle Williamson, GIS analyst with DLC Resources, looked over a roughly 1-acre common area (Sample 1) within a homeowners association (HOA). At this development, DLC Resources manages a variety of local climate-tolerant plant species such as Mesquite trees, Oleander shrubs and Lantana ground cover, in addition to areas covered by turf and decomposed granite.
This property appeared to have a higher plant density than most and Williamson wanted to put the density into an accurate perspective. The onsite data collection and input might have taken a couple of days using the conventional walk-around method, Williamson noted.
After the collection process, the data were exported from the hard drive of the computer in the pickup truck cab. Point cloud and photographic data were imported into Spatial Factory, which merges the imagery and LiDAR point cloud data “layers,” allowing Williamson to view, analyze and extract features from the data.
Williamson digitized the plantings, contrasting them with the background. She exported the digitized imagery as a shapefile and also calculated the plant density for DLC Resources’ water department. The density of a plant every 4.42 feet is medium-high compared with DLC Resources’ other properties. Defining variables specific to this property was critical to calculating the volume of water needed per acre.
End results
In a second sample area, the observed mean distance between plants, i.e., plant density, was 4.42 feet. Williamson calculated the area as 1.14 acres.
Comparing the plant density at this property compared with another of DLC’s communities, in the southeast valley of Phoenix, which has a much lower plant density, illustrates the importance of precisely calculating plant density for the purpose of optimizing water consumption. The highest plant density at the HOA in the southwest valley was 606 plants, compared with only 103 at the smaller of two samples at the HOA in the southeast valley. The higher density HOA needs 1.09 feet of water per acre whereas a lower density HOA needs only 0.19 feet of water per acre.
The higher-density HOA needs 355,179 gallons per acre, the lower-density only 60,368 gallons per acre. At an average water cost of $4 per 1,000 gallons, DLC Resources can estimate a water cost of about $1,421 per acre for the higher-density HOA and $241 for the lower-density HOA.
Don Talend of Write Results, West Dundee, Illinois, is a print and digital content producer specializing in covering construction, technology and innovation.