How the right maintenance, operation and site prep can keep your equipment out of the shop
Equipment should make a landscaper’s job easier and less physically tiring. But if a machine isn’t properly maintained and operated, it can cost owners some serious money and maybe even a client.
“During downtime, you’re losing money,” says Tony Weston, owner of Weston Lawn Equipment in Lawrenceville, Illinois. “If you can’t cut a customer’s lawn, they’ll find someone else who can.”
So how can landscapers cut back on mower downtime? Three landscapers offer their advice and say it all comes down to training, maintenance and scoping the site.
Know the ins and outs
Equipment is an investment, so landscapers shouldn’t just turn their machines over to inexperienced employees.
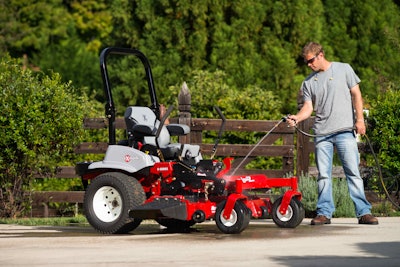
Doug Zepp, owner of Douglas Lawn and Landscaping in Westminster, Maryland, starts by giving operators on-the-job training. “We call them a rookie, and they go with an experienced worker to learn everything from loading the machine to safety, which is the main concern,” he says. “You can’t just send a guy right out of the gate.”
Zepp’s crews mainly use John Deere belly-mount mowers, which he says helps provide stability on hillsides, and they all learn the ins and outs of each job. “If you train everybody, anyone can fill in and do whatever’s needed at any given time,” Zepp says.
Weston, who has about 35 employees and handles commercial mowing accounts, also gives new workers real-life training. But, they don’t get on the mower until after they’re more seasoned – usually starting out being a trimmer.
“We let them go a little ways on the jobsite, explain what to do, see what their tendencies are and watch how they do on their own for a few days,” Weston explains. If they see the newbie has any unsafe or bad tendencies, they work to correct them.
Chris Shipp, owner of Shipp Shape Lawn Service in Sylvester, Georgia, starts his new workers out by handing them the owner’s manual for the mower. He also shows them a Grasshopper DVD tutorial on how they should maintain the mower, what to pay attention to when operating and daily machine checks. During his busy time, he has 11 employees.
Preventative maintenance
Maybe the most common reason for downtime, improper mower maintenance can cripple a fleet.
“Do your maintenance,” Weston urges. “If anything, do it more than what it says. If it says to change the oil every 50 hours, change it every 40 hours. There’s a reason those parameters are set.”
Crews should check the air filters, oil, blade, belts and pulleys before leaving the shop. “You don’t want to get to the jobsite and have the mower stop running,” Weston says. During the winter, owners should perform extensive maintenance to reduce shop time during the busy season.
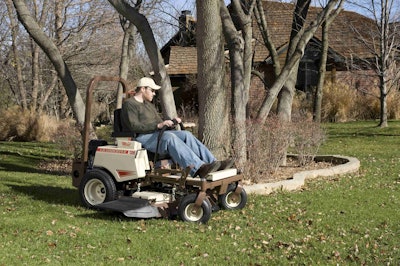
Weston has two, full-time mechanics who only work on the lawn-service equipment, which includes 24 mowers. He runs 18 mowers – which are split between six crews – full time and keeps the other ones at the shop as back up. “Downtime is a way of life,” he says. “It’s going to happen.” It’s also important to have a dealer that will guarantee downtime units, says Weston, who uses Exmark equipment.
Shipp does a complete maintenance work over every 100 hours but says the service time depends on the mower type and manufacturer. He suggests looking at the hourly meter on the machine and setting up a schedule based on that.
“When you’re having to run a mower every day, the maintenance schedule is the first thing you want to pay attention to,” Shipp says. He keeps track of each time the mower is worked on – whether it’s an oil change or greasing.
Every morning, the crew members do a walk around of their mower, with each having a dedicated machine. “You have a better ear for the machine when you use the same one every day,” Shipp says. “It also gives them pride and responsibility.”
Shipp, who focuses on municipal, commercial and residential properties, doesn’t change out mowers very often, using each for 4,000 to 5,000 hours. He currently has seven Grasshopper machines in his fleet, including front-mount, mid-mount and rear-discharge mid-mount mowers.
Zepp has a crew member who sharpens the blades, greases the machine and washes the mowers at the end of the day. “Then we just load up and go every morning,” he says.
Like the other landscapers, his team also follows a strict maintenance schedule, so “not only does it all look good on the job, we never have a problem getting rid of the used equipment,” says Zepp, who handles mostly commercial accounts.
He trades in his mowers every two to three years, in part because of advice his brother – who also had a landscaping business – gave him. “He would say, ‘A new payment is easier to make than a garage payment,’” Zepp recalls.
Know the lawn
Even the best maintenance schedule is no match for the wear and tear a jobsite can cause.
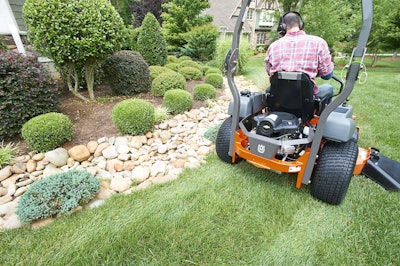
If it’s a crew’s first day on a property, they should scope out the lawn, Weston says. “There are always trouble spots,” he says. “Walk the yard, ask the customer if there’s anything there you need to know about and find any cables or wires.”
After the first walk through, crews should make notes of any objects found, such as stumps, stakes or holes. Instead of just leaving them, he has crews hammer down stakes and cut down stumps – preventing future problems. He also suggests using a higher blade level, 3 to 3 1/2 inches, the first time at an account until becoming comfortable with the terrain.
“Be on the lookout for limbs, rocks, nuts or anything else that could tear up the machine,” Weston says. “If you hit something, it can bend the brackets and throw the deck off.”
But before even stepping foot on the lawn, landscapers should make sure they purchase the right machine for the job, Shipp says.
“If you’re doing residential work, you want to have a machine that’s tailored to residential,” he says. “For commercial jobs, you need equipment that operates on a commercial level. The better the mower is equipped for the job, the less downtime you’ll have because it’s being used for the right application.”